Lamborghini går videre med smedet kulfiber
For femogtredive år siden revolutionerede McLaren både motorsport og bilverdenen som helhed. På baggrund af erfaringer fra rumfart introducerede McLaren den første Formel 1-racer med et kulfiberkompositbadekar (CFC) i stedet for en bundet og nittet aluminiumspladestruktur. Succesen med denne satsning muliggjorde igen den passende navngivne McLaren F1 sportsvogn, som havde en støbt CFC monocoque, der fungerede som passagerkabine og strukturel kerne.
Siden da er den teknologiske nedsivning fortsat, dryp for dryp, fra fly til racerbiler til superbiler og for nylig til overkommelige vejbiler. På dette års biludstilling i New York introducerede Toyota sin Prius Prime plug-in hybrid udstyret med en CFC-bagklap, hvilket muliggør en vægtbesparelse på otte pund i forhold til det standardstemplede og pletsvejsede stål.
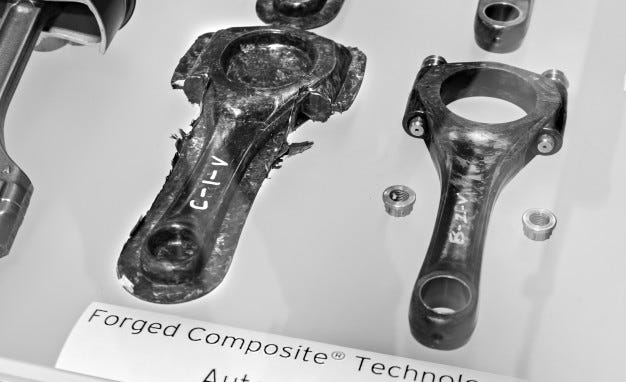
Feraboli havde en bedre idé: fjern autoklaven. Hvad han og Lamborghini patenterede som Forged Composites (FC) teknologi forenklede og fremskyndede støbeprocessen. Trin et: læg hakkede, tilfældigt orienterede kulfibre imprægneret med harpiks i en todelt stålform. Trin to: påfør varme og 1200 til 1500 psi tryk. Efter kun tre minutter er CFC-delen hærdet og klar til fjernelse fra formen og trimning. Det tog otte år at udvikle denne proces til at fremstille de omkring 1000 vinduesrammer, kiler og ribforstærkninger, der går ind i hver Boeing 787 Dreamliner. Den vanskelige del var at overbevise Federal Aviation Administration om, at denne fremstillingsmetode - begyndende med det, der kaldes hakket kulstofpladestøbningsforbindelse - er levedygtig. Overførsel af det fra 787 til Lamborghinis var forholdsvis let.
I 2010, på biludstillingen i Paris, afslørede Lamborghini konceptbilen Sesto Elemento for at fremvise sit FC-gennembrud. Det strukturelle karbad, udvendige paneler og affjedringskontrolarme - 80 procent af bilen efter vægt - blev fremstillet ved hjælp af FC-metoder.
Feraboli forlod UW i 2013 for at etablere Lamborghinis Advanced Composites Structural Laboratory (ACSL) i Seattles Interbay-distrikt. Denne 8000 kvadratmeter store facilitet, der i øjeblikket er bemandet med fem ansatte, samarbejder med et 60-personers Advanced Composites Research Center på Lamborghinis hjemmebase i Sant'Agata Bolognese, Italien. ACSL fremmer også kulfibersagen ved at udføre test for forskellige fly- og producenter af sportsudstyr, ved at gennemføre en- til fem-dages træningssessioner og ved at huse et skalamodel Lamborghini-museum.
Maurizio Reggiani, Lamborghini bestyrelsesmedlem med ansvar for R&D, kalder FC tech virksomhedens "arbejdshest", der i sidste ende vil tjene mange strukturelle, kropspaneler og kosmetiske trimbehov. Et problem, han står over for, er at markedsføre en anden æstetik - hvad der ligner mere marmor eller burl træ versus det traditionelle sorte vævede stof - til sine superbilvælgere. For at tilskynde til accept får Lamborghini allerede FC-dele til at infiltrere produktionsmodeller. Den første semistrukturelle komponent er et malet, aftageligt tagpanel til Aventador cabriolet. FC motorrum trim er tilgængelig som en $ 7000 option på Huracán . En indvendig pakke bestående af fire ventilationsåbninger, karmplader, dørtræk og midterkonsolbeklædning med FC-look under en blank klarlak vil snart blive tilbudt.
Den smedede del af FC-navnet kommer fra målet om at erstatte metalsmedninger i biler. Mens FC-affjedringskontrolarme og hjul er risikable, fordi det er svært at sige, hvornår de skal udskiftes på grund af hul eller kantstensangrebsskade, har ACSL FC-motorforbindelsesstænger i sit udstillingsvindue, der kan være tættere på at bære frugt. Den mest lovende kandidat leverer en vægtbesparelse på 39 procent i forhold til et design i smedet stål til den del.
Reggiani og Feraboli ville elske at se frugterne af deres arbejde omfavnet af andre mærker både inden for og uden for bilindustrien. Måske er det en tilfældighed, at Ferabolis daglige chauffør er en 2015 Corvette Stingray, men den næste generation af den sportsvogn virker som et ideelt sted at udvide FCs rækkevidde. Når man ved, hvor kræsen Corvette-ingeniørteamet er, hvis Lamborghinis teknologi tjener Chevys godkendelse til brug i den kommende Corvette med centermotor til 80.000 dollars , vil smedede kompositter være blevet plakatbarnet for omkostningseffektiv vægtbesparelse.
Gade: www.caranddriver.com