Lamborghini sta forgiando avanti con fibra di carbonio forgiata
Trentacinque anni fa, McLaren ha rivoluzionato sia gli sport motoristici che il mondo dell'auto in generale. Attingendo alle lezioni apprese dal settore aerospaziale, McLaren introdusse il primo pilota di Formula 1 con una vasca in fibra di carbonio-composito (CFC) al posto di una struttura in lamiera di alluminio incollata e rivettata. Il successo di quell'impresa a sua volta ha permesso l'auto sportiva McLaren F1, che aveva una monoscocca CFC stampata che fungeva da cabina passeggeri e nucleo strutturale.
Da allora, il trickle-down tecnologico è continuato, goccia a goccia, dagli aerei alle auto da corsa alle supercar e, recentemente, alle auto stradali a prezzi accessibili. Al salone dell'auto di New York di quest'anno, Toyota ha presentato la sua Prius Prime ibrida plug-in dotata di un portellone posteriore CFC, che consente un risparmio di peso di otto libbre rispetto all'acciaio standard stampato e saldato a punti.
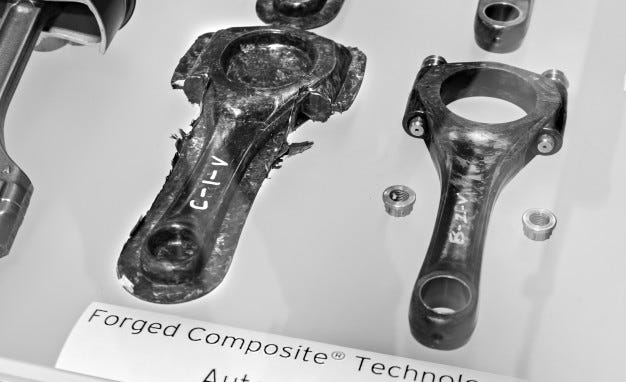
Feraboli ebbe un'idea migliore: eliminare l'autoclave. Quella che lui e Lamborghini hanno brevettato come tecnologia Forged Composites (FC) ha semplificato e accelerato il processo di stampaggio. Fase uno: caricare le fibre di carbonio tritate e orientate in modo casuale impregnate di resina in uno stampo in acciaio in due pezzi. Fase due: applicare calore e pressione da 1200 a 1500 psi. Dopo soli tre minuti, la parte CFC è indurita e pronta per la rimozione dallo stampo e la rifilatura. Ci sono voluti otto anni per sviluppare questo processo per realizzare i circa 1000 telai dei finestrini, i soffietti e i rinforzi delle nervature che entrano in ogni Boeing 787 Dreamliner. La parte difficile è stata convincere la Federal Aviation Administration che questo metodo di produzione, a partire da quello che viene chiamato composto per lo stampaggio di fogli di carbonio tritati, è praticabile. Trasferirla dalla 787 alla Lamborghini è stato relativamente facile.
Nel 2010, al salone dell'auto di Parigi, Lamborghini ha presentato 012753 la concept car Sesto Elemento 012751 per mostrare la sua svolta FC. La vasca strutturale, i pannelli esterni e i bracci di controllo delle sospensioni, l'80% del peso dell'auto, sono stati realizzati con metodi FC.
Feraboli ha lasciato UW nel 2013 per fondare l'Advanced Composites Structural Laboratory (ACSL) di Lamborghini nel quartiere Interbay di Seattle. Questa struttura di 8000 piedi quadrati, attualmente con cinque dipendenti, è in contatto con un Centro di Ricerca sui Compositi Avanzati di 60 persone presso la sede di Lamborghini a Sant'Agata Bolognese, in Italia. ACSL promuove anche la causa della fibra di carbonio eseguendo test per vari produttori di aeromobili e attrezzature sportive[012754 012751], conducendo sessioni di formazione da uno a cinque giorni e ospitando un museo Lamborghini in scala.
Maurizio Reggiani, membro del consiglio di amministrazione di Lamborghini responsabile della ricerca e sviluppo, definisce FC tech il "cavallo di battaglia" dell'azienda che alla fine soddisferà molte esigenze strutturali, di pannelli della carrozzeria e di finiture estetiche. Un problema che deve affrontare è la commercializzazione di un'estetica diversa, che assomiglia più al marmo o al legno di radica rispetto al tradizionale tessuto nero, per i suoi elettori di supercar. Per incoraggiarne l'accettazione, Lamborghini sta già facendo infiltrare parti di FC nei modelli di produzione. Il primo componente semi-strutturale è un pannello del tetto verniciato e rimovibile per l'Aventador cabriolet. L'allestimento del vano motore FC è disponibile come opzione da $ 7000 su la Huracán. Presto sarà offerto un pacchetto interno composto da quattro bocchette di aerazione, battitacca, maniglie delle portiere e finiture della console centrale con il look FC sotto un rivestimento trasparente lucido.
La parte forgiata del nome FC deriva dall'obiettivo di sostituire i forgiati metallici nelle auto. Mentre i bracci di controllo e le ruote delle sospensioni FC sono rischiosi perché è difficile dire quando devono essere sostituiti a causa di buche o lesioni da marciapiede, l'ACSL ha bielle del motore FC nella sua vetrina che potrebbero essere più vicine alla realizzazione. Il candidato più promettente offre un risparmio di peso del 39% rispetto a un design in acciaio forgiato per quella parte.
Reggiani e Feraboli vorrebbero vedere i frutti del loro lavoro abbracciati da altri marchi sia all'interno che all'esterno dell'industria automobilistica. Forse è una coincidenza che l'autista quotidiano di Feraboli sia una Corvette Stingray del 2015, ma la prossima generazione di quell'auto sportiva sembra il luogo ideale per estendere il raggio d'azione di FC. Sapendo quanto sia esigente il team di ingegneri della Corvette, se la tecnologia di Lamborghini otterrà l'approvazione di Chevy per l'uso 012756 nella prossima Cor 012751 vette a motore centrale da 80.000 dollari, i compositi forgiati saranno diventati il manifesto per il risparmio di peso a costi contenuti.
Via: www.caranddriver.com