Lamborghini setzt auf geschmiedete Kohlefaser
Vor 35 Jahren revolutionierte McLaren sowohl den Motorsport als auch die Autowelt insgesamt. Basierend auf den Erfahrungen aus der Luft- und Raumfahrt stellte McLaren den ersten Formel-1-Rennwagen mit einer Wanne aus Kohlefaserverbundwerkstoff (CFC) anstelle einer geklebten und genieteten Aluminiumblechstruktur vor. Der Erfolg dieses Unterfangens ermöglichte wiederum den treffend benannten McLaren F1-Sportwagen, der über ein geformtes CFC-Monocoque verfügte, das als Passagierkabine und struktureller Kern diente.
Seitdem hat sich der technologische Trickle-Down tröpfchenweise fortgesetzt, von Flugzeugen über Rennwagen bis hin zu Supersportwagen und seit kurzem auch erschwinglichen Straßenautos. Auf der diesjährigen New York Auto Show stellte Toyota seinen Prius Prime Plug-in-Hybrid vor, der mit einer CFC-Heckklappe[012751 ausgestattet ist, die eine Gewichtseinsparung von acht Pfund gegenüber dem standardmäßigen gestanzten und punktgeschweißten Stahl ermöglicht.
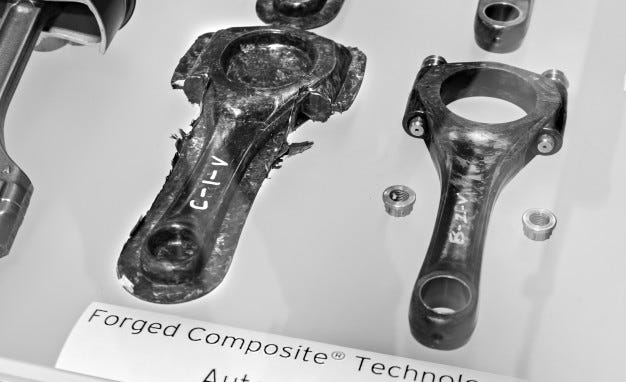
Feraboli hatte eine bessere Idee: den Autoklaven zu eliminieren. Was er und Lamborghini als Forged Composites (FC)-Technologie patentierten, vereinfachte und beschleunigte den Formgebungsprozess. Schritt eins: Zerkleinerte, zufällig ausgerichtete Carbonfasern, die mit Harz imprägniert sind, in eine zweiteilige Stahlform laden. Schritt zwei: Wenden Sie Wärme und 1200 bis 1500 psi Druck an. Nach nur drei Minuten ist das CFC-Teil ausgehärtet und bereit für die Entnahme aus der Form und den Beschnitt. Es dauerte acht Jahre, um dieses Verfahren zu entwickeln, um die rund 1000 Fensterrahmen, Zwickel und Rippenverstärkungen herzustellen, die in jeden Boeing 787 Dreamliner eingebaut werden. Der schwierige Teil bestand darin, die Federal Aviation Administration davon zu überzeugen, dass diese Herstellungsmethode – beginnend mit der so genannten Sheet-Sheet-Moulding-Compound aus gehacktem Kohlenstoff – praktikabel ist. Der Transfer von der 787 zu Lamborghinis war vergleichsweise einfach.
Im Jahr 2010 enthüllte Lamborghini auf dem Pariser Autosalon das Konzeptfahrzeug Sesto Elemento, um seinen FC-Durchbruch zu demonstrieren. Die strukturelle Wanne, die Außenverkleidungen und die Querlenker der Aufhängung – 80 Prozent des Gewichts des Fahrzeugs – wurden mit FC-Methoden hergestellt.
Feraboli verließ die UW im Jahr 2013, um das Advanced Composites Structural Laboratory (ACSL) von Lamborghini im Stadtteil Interbay in Seattle zu gründen. Diese 8000 Quadratmeter große Einrichtung, die derzeit mit fünf Mitarbeitern besetzt ist, steht in Verbindung mit einem 60-köpfigen Advanced Composites Research Center am Heimatstandort von Lamborghini in Sant'Agata Bolognese, Italien. ACSL fördert auch die Sache der Kohlefaser, indem es Tests für verschiedene Flugzeug- und Sportgerätehersteller durchführt, ein- bis fünftägige Schulungen durchführt und ein maßstabsgetreues Lamborghini-Museum beherbergt.
Maurizio Reggiani, Lamborghini-Vorstandsmitglied, das für Forschung und Entwicklung verantwortlich ist, bezeichnet die FC-Technologie als das "Arbeitspferd" des Unternehmens, das letztendlich viele Anforderungen an Struktur, Karosserieteile und kosmetische Verkleidungen erfüllen wird. Ein Problem, mit dem er konfrontiert ist, ist die Vermarktung einer anderen Ästhetik – die eher nach Marmor oder Wurzelholz aussieht als nach dem traditionellen schwarzen Webstoff – für seine Supersportwagen-Bestandteile. Um die Akzeptanz zu fördern, lässt Lamborghini bereits FC-Teile in Serienmodelle einfließen. Das erste halbstrukturelle Bauteil ist eine lackierte, abnehmbare Dachplatte für das Aventador Cabriolet[012751 012755]. Die FC-Motorraumverkleidung ist als 7000-Dollar-Option für den Huracán erhältlich. Demnächst wird ein Interieur-Paket bestehend aus vier Luftausströmern, Schwellerblechen, Türgriffen und Mittelkonsolenverkleidungen in FC-Optik unter glänzendem Klarlack angeboten.
Der geschmiedete Teil des Namens FC stammt von dem Ziel, Metallschmiedeteile in Autos zu ersetzen. Während FC-Querlenker und -Räder riskant sind, weil es schwierig ist, zu sagen, wann sie aufgrund von Schlaglöchern oder Bordsteinverletzungen ausgetauscht werden müssen, hat der ACSL FC-Motorpleuel in seinem Schaufenster, die näher an der Verwirklichung sein könnten. Der vielversprechendste Kandidat bietet für dieses Teil eine Gewichtseinsparung von 39 Prozent gegenüber einer Schmiedestahlkonstruktion.
Reggiani und Feraboli würden gerne sehen, wie die Früchte ihrer Arbeit von anderen Marken innerhalb und außerhalb der Automobilindustrie angenommen würden. Vielleicht ist es ein Zufall, dass Ferabolis täglicher Fahrer eine 2015er Corvette Stingray ist, aber die nächste Generation dieses Sportwagens scheint ein idealer Ort zu sein, um die Reichweite des FC zu erweitern. Wenn man weiß, wie wählerisch das Corvette-Ingenieursteam ist, wenn Lamborghinis Technologie die Genehmigung von Chevy für den Einsatz 012756 in der kommenden 80.000 US-Dollar teuren Mittelmotor-Corvette[012751 erhält, werden geschmiedete Verbundwerkstoffe zum Aushängeschild für kostengünstige Gewichtseinsparungen werden.
Straße: www.caranddriver.com