Lamborghini está forjando con fibra de carbono forjada
Hace treinta y cinco años, McLaren revolucionó tanto el automovilismo como el mundo del automóvil en general. Basándose en las lecciones aprendidas de la industria aeroespacial, McLaren presentó el primer corredor de Fórmula 1 con una bañera de compuesto de fibra de carbono (CFC) en lugar de una estructura de chapa de aluminio unida y remachada. El éxito de esa empresa a su vez permitió el bien llamado McLaren F1 coche deportivo, que tenía un CFC monocasco moldeado que sirve como su cabina de pasajeros y el núcleo estructural.
Desde entonces, el goteo tecnológico ha continuado, goteo por goteo, desde aviones hasta autos de carrera, superdeportivos y, recientemente, hasta autos de carretera asequibles. En el Auto Show de Nueva York de este año, Toyota presentó su Prius Prime híbrido enchufable equipado con una escotilla trasera CFC , Lo que permite un ahorro de peso de ocho libras sobre el acero estándar estampado y soldado por puntos.
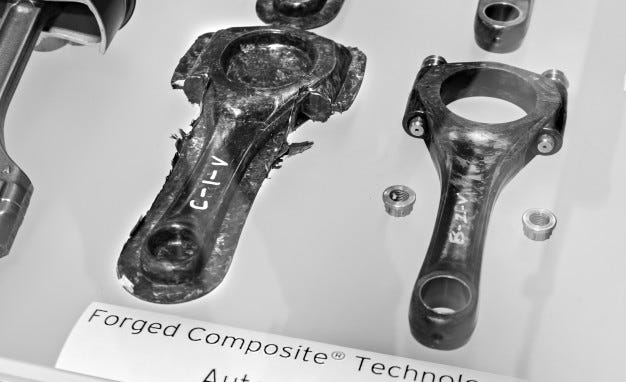
Ferabólico tuvo una idea mejor: eliminar el autoclave. Lo que él y Lamborghini patentaron como Tecnología forjada de los compuestos (FC) Simplificado y acelerado el proceso de moldeo. Paso uno: cargue las fibras de carbono picadas, orientadas aleatoriamente impregnadas con la resina en un molde de acero de dos piezas. Paso dos: aplique calor y 1200 a 1500 psi de presión. Después de sólo tres minutos, la pieza de CFC está curada y lista para ser retirada del molde y recortada. Se tardó ocho años en desarrollar este proceso para hacer los aproximadamente 1000 marcos de ventanas, refuerzos y refuerzos de costillas que entran en cada Boeing 787 Dreamliner. La parte difícil fue convencer a la Administración Federal de Aviación de que este método de fabricación, comenzando con lo que se llama compuesto de moldeo de láminas de carbono picado, es viable. Transferirlo del 787 a Lamborghinis fue relativamente fácil.
En 2010, en el Salón del Automóvil de París, Lamborghini El coche de concepto de Sesto Elemento Para mostrar su avance FC. La bañera estructural, los paneles exteriores y los brazos de control de la suspensión, el 80 por ciento del peso del automóvil, se fabricaron utilizando métodos FC.
Ferabólico dejó UW en 2013 para establecer el Laboratorio Estructural de Compuestos Avanzados (ACSL) de Lamborghini en el distrito de Interbay de Seattle. Esta instalación de 8000 pies cuadrados, actualmente con cinco empleados, está en contacto con un Centro de Investigación de Compuestos Avanzados de 60 personas en la base de Lamborghini en Sant'Agata Bolognese, Italia. ACSL también avanza la causa de fibra de carbono mediante la realización de pruebas para varias aeronaves y Fabricantes de equipamiento deportivo , Llevando a cabo sesiones de entrenamiento de uno a cinco días, y albergando un museo Lamborghini modelo a escala.
Maurizio Reggiani, miembro de la junta de Lamborghini responsable de I + D, llama a FC tech el "caballo de batalla" de la compañía que eventualmente servirá para muchas necesidades estructurales, de paneles de carrocería y adornos cosméticos. Un problema que enfrenta es la comercialización de una estética diferente, lo que se parece más a mármol o madera burl frente a la tela tejida negra tradicional, para sus componentes de superdeportivo. Para fomentar la aceptación, Lamborghini ya está haciendo que las piezas FC se infiltren en los modelos de producción. El primer componente semiestructural es un panel de techo pintado y extraíble para El Aventador Convertible . El ajuste de la bahía del motor FC está disponible como una opción de $7000 en El Huracán . Pronto se ofrecerá un paquete interior que consta de cuatro salidas de aire, placas de umbral, tiradores de puertas y molduras de consola central con el aspecto FC bajo una capa transparente brillante.
La parte forjada del nombre de FC proviene del objetivo de reemplazar las piezas forjadas de metal en los automóviles. Mientras que los brazos y las ruedas de control de la suspensión FC son riesgosos porque es difícil saber cuándo necesitan ser reemplazados debido a una lesión en el agujero o en el bordillo, el ACSL tiene bielas del motor FC en su escaparate que pueden estar más cerca de realizarse. El candidato más prometedor ofrece un 39 por ciento de ahorro de peso sobre un diseño de acero forjado para esa parte.
A Reggiani y Feraboni les encantaría ver los frutos de su trabajo en otras marcas, tanto dentro como fuera de la industria automotriz. Tal vez sea una coincidencia que el conductor diario de Ferabólico sea un Corvette Stingray 2015, pero la próxima generación de ese automóvil deportivo parece un lugar ideal para extender el alcance de FC. Sabiendo lo exigente que es el equipo de ingeniería de Corvette, si la tecnología de Lamborghini obtiene la aprobación de Chevy para su uso en Corvette de motor central de 80.000 dólares , Los compuestos forjados se habrán convertido en el niño del cartel para el ahorro de peso rentable.
Vía: www.caranddriver.com